What is Dynamic Buffer Management?
Dynamic Buffer Management (DBM): Smarter Inventory Control Without Forecasting
Dynamic Buffer Management (DBM) is a proven inventory management method that continuously adjusts buffer levels based on actual demand and supply conditions. Instead of relying on static reorder points or forecasts, DBM automatically increases, decreases, or maintains stock buffers to keep inventory flowing efficiently.
How It Works
DBM classifies inventory On Hand into three buffer zones:
🟢 Green – Stock is stable, no action needed.
🟡 Yellow – Reorder soon, demand is increasing.
🔴 Red – Urgent, risk of stockout.
By monitoring consumption patterns and supply variability, DBM dynamically adjusts these buffer levels:
✔ If demand increases consistently → Buffer size increases to prevent stockouts.
✔ If demand slows down → Buffer size decreases to reduce excess inventory.
Why DBM?
✅ No Guesswork – Adjusts in real time, avoiding forecast-driven mistakes.
✅ Improves Service Levels – Ensures NOOS (Never Out of Stock) products stay available.
✅ Frees Up Working Capital – Cuts unnecessary inventory without increasing risk.
✅ Fast & Scalable – Works across categories, from apparel to consumables.
DBM is not a black-box system. It’s a well-established, publicly available methodology used across industries to improve inventory performance—without requiring AI, machine learning, or expensive software.
At Retail Twin Labs, we apply a refined, execution-focused version of DBM to help businesses optimize their NOOS inventory strategies or to see how we can help your supply chain become more responsive and profitable. 🚀Dynamic Buffer Management (DBM) is a smart way to meet demand without overstocking. DBM is part of Dr. Eli Goldratt’s Theory of Constraints, which focuses on flow principles to get goods to where they are needed, whether at a distribution center (DC) or points of use or sale, without wasting resources.
Unlike inventory management based on a forecast that might miss the mark, DBM uses the responsiveness of the system as a whole. It watches how fast your goods are moving and adjusts buffers based on what’s really happening.
The Buffer Zones:
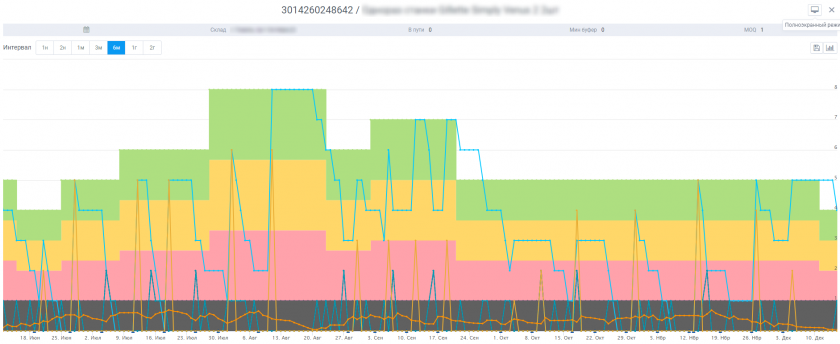
- Green Zone: Your safe spot. Stock is plenty, demand is steady, and you’re covered. If you’re always in green, though, you have too much—DBM could shrink the buffer to free up space or cash.
- Yellow Zone: The “pay attention” zone. Stock’s dipping a bit, and you’re using the buffer. It’s a heads-up to maybe reorder or check demand trends—no rush, just stay alert.
- Red Zone: The urgent zone. Stock is low, and you’re at risk of running out. DBM will likely increase the buffer to keep stock flowing.
Why it works:
DBM is great for items with long shelf lives, such as 'never out of stock' merchandise like cosmetics, hardware, or over the counter (OTC) pharmaceuticals—where lead times (how long it takes to restock) are short compared to how long the product is used or offered to consumers. DBM is about remaining responsive to real demand and supply, not dependent on that elusive perfect prediction.
DBM is not for everything. Fashion items, for example, tend to have a low lead-time-to-shelf-life ratio, and their demand may be affected by many more inputs, like short term trends, the weather, and local consumer sentiments. Here, DBM’s responsiveness can lag, and predictive inventory management and AI shines instead, using forecasts and the relative importance of each input to predict what will sell.
Stop guessing. Start responding. Stay in control.
Curious about how much better your supply chain could perform? Let’s find out together. Send an Email to hello@retailtwin.com, or schedule a call via the calendar link below. I look forward to helping you achieve supply chain excellence.
đź“… Schedule a call or email hello@retailtwin.com.
Stay ahead of the curve! Subscribe for insights.